1부: 기어 및 자동차 서스펜션 부품
1. 기어 가공 공정
다른 구조적 요구 사항에 따라 기어 부품 가공의 주요 기술 프로세스는 블랭크 단조 → 정상화 → 마무리 가공 → 기어 성형 → 모따기 → 호빙 → 면도 → (용접) → 열처리 → 연삭 → 메쉬 트리밍입니다.
메인 및 보조 치아 또는 고객이 치아를 연마하는 데 필요한 부품을 제외하고 일반적으로 치아는 가열 후 가공되지 않습니다.
2. 샤프트 공정 흐름
입력 샤프트: 단조 빌릿 → 노멀라이징 → 마무리 가공 → 톱니 압연 → 드릴링 → 톱니 성형 → 모따기 → 호빙 → 면도 → 열처리 → 연삭 → 맞물림 트리밍.
출력 샤프트: 단조 빌릿→정규화→마무리 가공→연삭 및 호빙→면도→열처리→연삭→페어링 트림.
3. 구체적인 프로세스 흐름
(1) 빌렛 단조
열간 단조는 자동차 기어 부품에 널리 사용되는 블랭크 단조 공정입니다. 과거에는 열간 단조 및 냉간 압출 블랭크가 널리 사용되었습니다. 최근에는 샤프트 가공에서 크로스 쐐기 압연 기술이 널리 추진되고 있습니다. 이 기술은 복잡한 계단식 샤프트용 블랭크 제작에 특히 적합합니다. 그것은 높은 정밀도, 작은 후 처리 허용량뿐만 아니라 높은 생산 효율성을 가지고 있습니다.
(2) 정규화
이 공정의 목적은 후속 기어 절단에 적합한 경도를 얻고 최종 열처리를 위한 구조를 준비하여 열처리 변형을 효과적으로 줄이는 것입니다. 일반 노멀라이징은 인력, 장비 및 환경의 영향을 크게 받아 공작물의 냉각 속도 및 균일성을 제어하기 어려워 경도 분산이 크고 금속 조직이 고르지 않아 가공 및 최종 열처리에 직접적인 영향을 미칩니다.
(3) 마무리 가공
고정밀 기어 가공의 포지셔닝 요구 사항을 충족하기 위해 CNC 선반은 기어 블랭크의 마무리에 사용됩니다. 기어의 내부 구멍과 위치 결정 단면이 먼저 가공된 다음 다른 쪽 끝면과 외경의 가공이 동시에 완료됩니다. 그것은 내부 구멍과 포지셔닝 단면의 수직 요구 사항을 보장할 뿐만 아니라 대규모 치아 블랭크 생산의 크기 분산이 작은 것을 보장합니다. 따라서 기어 블랭크의 정밀도가 향상되고 후속 기어의 가공 품질이 보장됩니다.
샤프트 부품 가공을 위한 포지셔닝 및 클램핑에는 세 가지 주요 방법이 있습니다.
1. 공작물의 중심 구멍으로 위치 결정 : 샤프트 가공에서 부품의 각 외면과 단면의 동축도와 회전축에 대한 단면의 수직도가 상호 위치의 주요 항목입니다. 정확성. 이러한 표면의 설계 기준은 일반적으로 둘 다 샤프트의 중심선입니다. 두 개의 중앙 구멍을 위치 지정에 사용하는 경우 데이텀 일치의 원칙을 따릅니다.
2. 바깥쪽 원과 중심 구멍은 위치 기준으로 사용됩니다(하나의 클램프와 하나의 상단): 센터링 정확도는 높지만 강성이 낮습니다. 특히 무거운 공작물을 처리할 때 충분히 안정적이지 않으며 절단 금액이 너무 커서는 안됩니다. 황삭 가공 중에 부품의 강성을 향상시키기 위해 샤프트의 외부 표면과 중앙 구멍을 가공 위치 지정 기준으로 사용할 수 있습니다. 이 위치 결정 방법은 큰 절삭 모멘트를 견딜 수 있으며 샤프트 부품의 가장 일반적인 위치 결정 방법입니다.
3. 2개의 외부 원형 표면을 위치 기준으로 사용: 중공축의 내부 구멍을 가공할 때(예: 모스 테이퍼의 내부 구멍을 공작 기계에 가공), 중심 구멍을 위치 기준으로 사용할 수 없습니다. , 그리고 샤프트의 두 외부 원형 표면은 위치 지정 기준으로 사용할 수 있습니다. 포지셔닝 데이텀. 공작물이 공작 기계의 스핀들 인 경우 두 개의지지 저널 (조립 기준)이 종종 위치 지정 기준으로 사용되어지지 저널에 대한 테이퍼 구멍의 동축을 보장하고 오정렬로 인한 오류를 제거 할 수 있습니다. 데이터의.
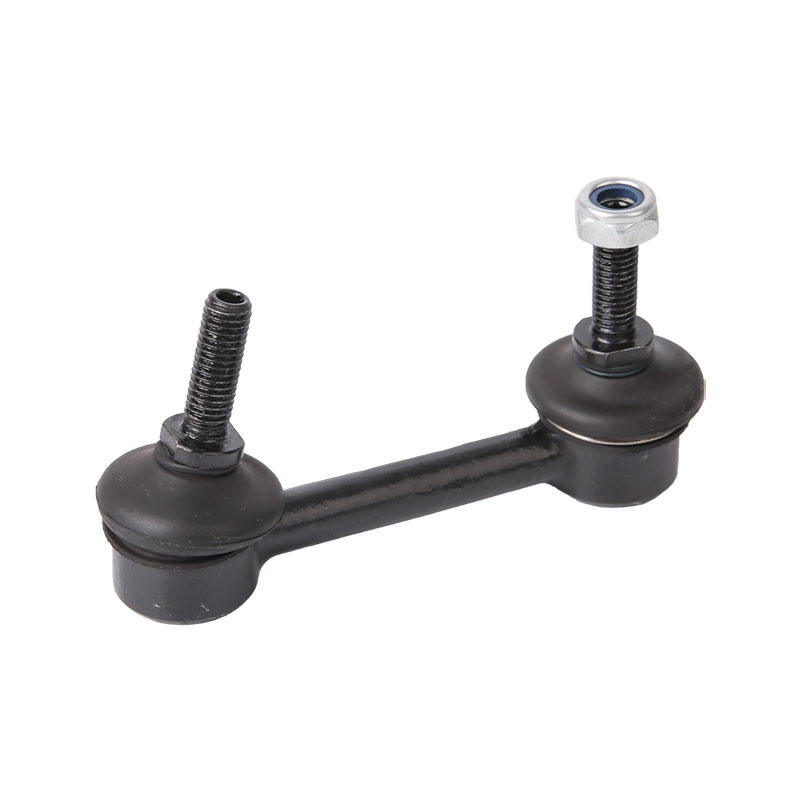
2부: 쉘 부품
1. 프로세스 흐름
일반적인 공정 흐름은 밀링 조인트 표면 → 가공 공정 구멍 및 연결 구멍 → 거친 보링 베어링 구멍 → 미세 보링 베어링 구멍 및 핀 구멍 찾기 → 청소 → 누출 테스트 감지입니다.
2. 제어 방법
(1) 비품
트랜스미션 하우징의 가공 공정은 "수직형 머시닝 센터 가공. 10# 공정 수직형 머시닝 센터 가공 20# 공정 수평형 머시닝 센터 가공 30# 공정"의 예를 들어, 공작물을 피하기 위해 3세트의 머시닝 센터 고정구가 필요합니다. 도구 간섭, 유연한 작동, 여러 조각 및 하나의 클램프, 빠른 전환과 같은 클램핑 변형도 고려해야 합니다.
(2) 도구 측면
자동차 부품 제조원가에서 공구비는 전체 원가의 3~5%를 차지한다. 모듈러 구조의 복합공구는 고정밀, 재사용이 가능한 공구홀더, 소량의 재고가 특징이며 널리 사용됩니다. 처리 시간을 크게 단축하고 노동 효율성을 향상시킬 수 있습니다. 따라서 정밀도 요구 사항이 높지 않고 표준 도구가 더 나은 처리 결과를 얻을 수 있는 경우 표준 도구를 최대한 사용하여 재고를 줄이고 호환성을 개선해야 합니다. 동시에 대량 생산 부품의 경우 고정밀 요구 사항이 필요한 부품에 고급 비표준 복합 도구를 사용하면 가공 정확도와 생산 효율성이 향상될 수 있습니다.